More than 35 years of plastic injection molding expertise
Windmill Plastics is a turnkey addition to your manufacturing capacity.
When you need to increase your molding and manufacturing capacity, we are a partner you can rely on for high-quality, low-cost molding, assembly, packaging and transport of your parts.
Mission
Provide our customers efficient, flexible, turnkey manufacturing of high quality injection molded parts.
Where we started
Windmill Plastics was founded in 1985 by a group of former Tupperware employees, making durable plastics part of the company’s DNA. Since then, our Knowlton, Québec, facility has grown from 15,000 square feet to 50,000 square feet.
For over 35 years, we have focused on molding products for some of North America’s largest houseware, toy, and transport companies, and Windmill Plastics grew to be one of Québec’s largest injection molders.
Where we’re going
In 2012, Windmill Plastics was bought by the Desrosiers family. A true family affair, Réjean Desrosiers and his sons François and Erik Desrosiers have combined their expertise in management, operations, accounting, and logistics to modernize the facility, increase capacity, and expand the company’s service offering.
In 2013, immediately after purchasing the company, we added 12 dedicated railway sidings in nearby Cowansville, Québec, along with a resin tanker to ensure additional capacity and a steady supply of plastic to our facility.
Then we turned our attention to automation. We added our first robot in 2015 and have since added 18 more. These robots handle repetitive tasks, freeing up our employees for the more skilled jobs. The robots also allow us to maintain a full production schedule round the clock, 365 days a year, making our output reliable.
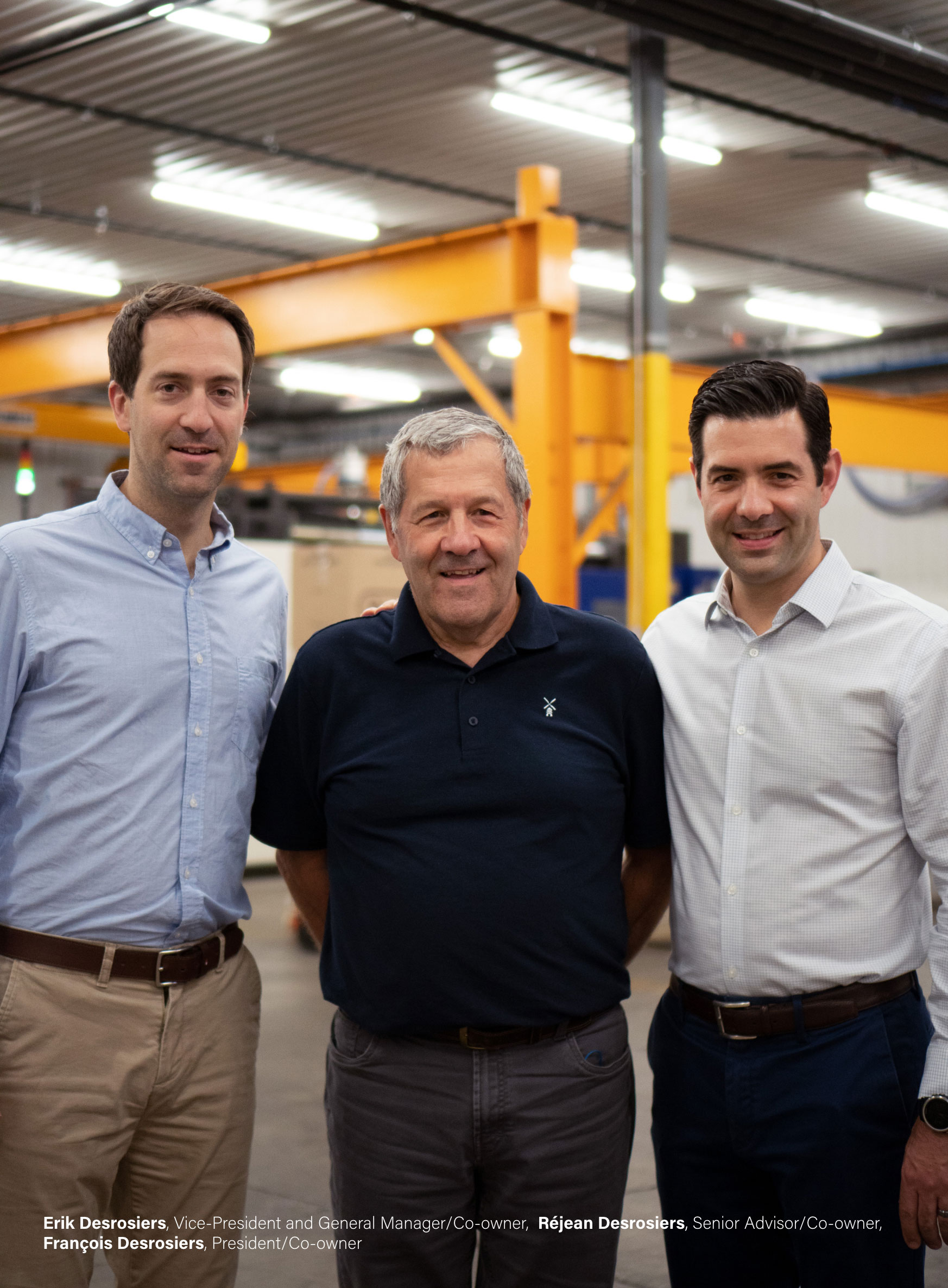
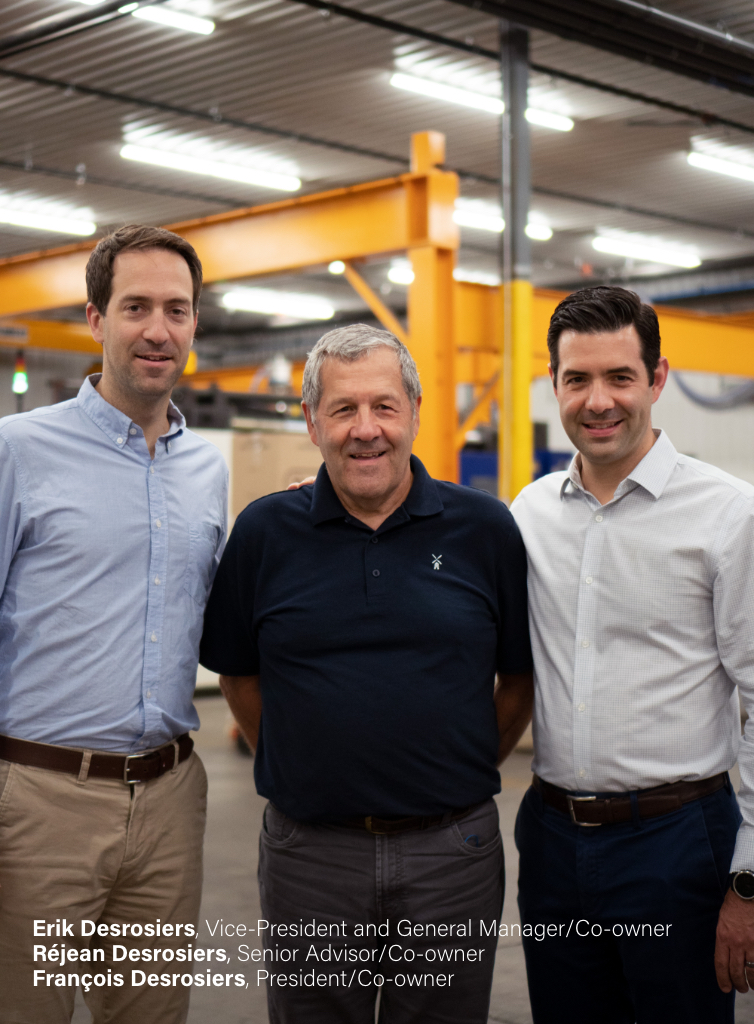
Over the past few years we have expanded our facility and added a number of new state of the art injection molding presses to the factory floor – notably a 1,500 ton machine a 1,200 to machine, another 1,000 ton machine and a number of 500 – 700 ton machines.
Going forward, we remain committed to continuing to renew our fleet of presses and to further automating our production, so we can continue to offer the highest efficiency and quality to our customers.
Mission
Provide our customers efficient, flexible, turnkey manufacturing of high quality injection molded parts.
Values
Well being: ‘’We provide stable careers in a safe work environment that encourage
work life balance.’’
Quality: ‘’We do not compromise on product quality.’’
Efficiency: ‘’We are focused on efficiently using our time, supplies, human and financial resources.’’
Fairness: ‘’We are all accountable for our words and actions, honest and fair in our dealings with one another.’’
Teamwork: ‘’We succeed as a team, by being welcoming, accessible and helping one another.’’
Vision
Continually evolve to be a state-of-the-art manufacturer that is an employer of choice in the region and an important citizen of our community.